いよいよ樹脂を使ってのFRPの積層作業
下面が紙粘土で失敗したので勇気を出してボディーから直接作ります。
付いてるカバーのリベットをドリルで芯を抜いて
カバーはッポイ(笑)
面の脱脂をしてアルミテープを下から貼って
さらにその上に塗装用マスキングテープを下から貼ります。
樹脂がはみ出てもいいように欲しい部分より大きめに貼りました。
この面のしわや起伏が直接FRPに転写されるので
可能な限り綺麗に・・・
(テープの重なりの段差は仕方ないのです)
樹脂が飛んだり垂れたりしたときの為に
テープ付きビニールテープ いわゆるマスカーを貼り付け
次に積層後にFRPが剥離しやすいように
マスキングテープの上からボンリースを塗って
乾いてはふき取ってまた塗ってを3~5回繰返しました。
でその上にPVAを同じように数回塗りこみました。
これで下準備完了
いよいよ積層ですがこれも下準備が・・・
まず強度の要となるガラスマットをある程度の形に切断しておいて
そして揉みまくる!
(形状に沿い易くする為です)
ガラス繊維が多少抜け落ちますが気にしない
この時点ではまだ大丈夫ですが、硬化するとガラス繊維が皮膚に
刺さったり吸い込んだりしてよろしくないので
保護めがね・保護マスクを付けましょう。
刷毛などの洗浄用にアセトンも用意
メインの樹脂ですが
ポリエステル樹脂(ノンパラ)を50g用意
それに硬化剤を基本100:1の割合(温度・湿度により変わります)で
硬化剤0.5gを樹脂に入れて割り箸で攪拌
ここからは時間との勝負なので素早く(笑)
ガラスマットを置いてその上から刷毛を使って樹脂を塗り捲り♪
空気が入らないように丁寧かつ大胆に素早く
樹脂がガラスマットに染み込んでいくと形状に馴染んできます。
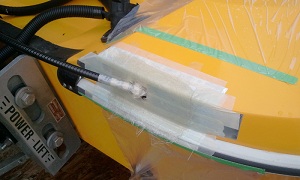
(見にくいですが色が変わってる部分が樹脂が染み込んだガラスマット)
馴染みにくい所はひたすら樹脂で攻撃・・・
全体が落ち着いたら刷毛や脱泡ローラーを使って余分な樹脂をシゴキながら気泡抜き
後は待つだけ♪
この時期気温も30℃以上になるので早起きしてやりましたが
慣れない作業でバタバタの汗ダクダク
硬化剤を混ぜた樹脂は固まる時に結構熱を持ちます。
容器に余った樹脂を容器越しに触ってみましたがかなり発熱してました。
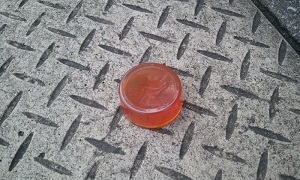
(容器内で固まった樹脂です)
でこの時期だと1時間もすれば十分に硬化してそうだったので剥離作業
ドキドキでしたが端っこにヘラを差し込んだら
ペリっと簡単に剥がれてくれました♪
何も無い所から形になって結構感激です。
ボディー側にも特にダメージも見当たらず。
あとはボディーに合わせながら余分なところをトリミングして完了
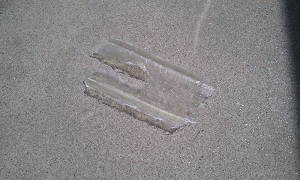
(写真はトリミング前の状態)
半硬化状態ならハサミでも十分切れるみたいです。
硬化後だったのでトリミングにはリューター・ヤスリ・グラインダー・金ノコで。
今回は1枚だけの積層 いわゆる1プライだったのですが
取り付け面としては1プライで十分な強度でした。
取り付け面は微妙な曲面だったのですが直取りなのでフィッティングも良好です。
次回は上物の積層
関連記事